INTRODUCTION TO REVERSE OSMOSIS MEMBRANE TECHNOLOGY
- Filtration Methods
The specification of different filtration methods such as size separation, target types, operating pressure, and application are summarized in the table below.
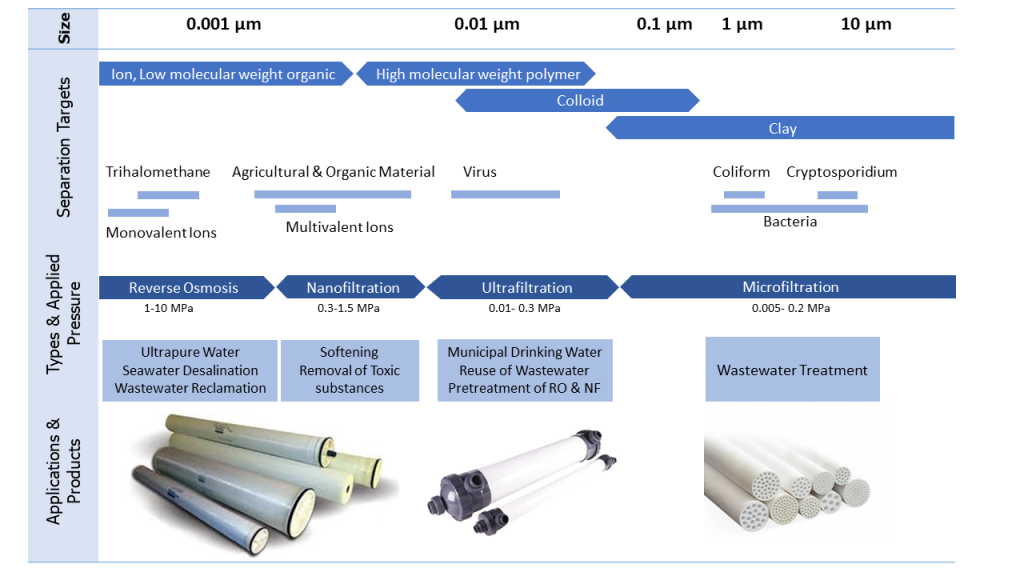
Reverse osmosis membranes, RO, have a surface active layer made of polyamide with a highly intertwined structure and approximate hole diameter of 0.0001 to 0.001 microns, which are used to remove soluble salts in water. Reverse osmosis membranes allow water molecules to pass through, but restrict the passage of other molecules.
Reverse osmosis membranes can be used to desalinate seawater and purify groundwater to produce drinking water. It can also be used to make ultrapure water for industrial applications such as the electronics industry, pharmaceutical industry, chemical process wastewater treatment and industrial wastewater recycling, boiler feed water, food and beverage industry applications, and power plant cooling water. In addition to soluble salts removal, these membranes also remove bacteria, viruses, pathogens and organic pollutants.
- Reverse Osmosis Membrane Process
When seawater and pure water are in the vicinity of a semi-permeable membrane, the water molecules flow toward the solution with higher concentration through the membrane. This natural phenomenon is called the “osmosis process”. Osmotic pressure is the driving force for the flow of pure water toward seawater inside the membrane, which is caused by the concentration difference on two sides of the membrane surface.
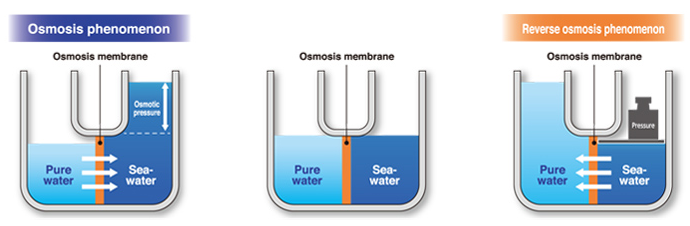
In general, the osmotic membrane or semipermeable membrane partly allows the transfer of the dissolved substances in the solution. The pressure at which molecules pass through the membrane is known as osmotic pressure. To keep the liquid level equal on both sides of the membrane, it is necessary to apply an external pressure equal to the osmotic pressure. When a pressure higher than the “osmotic pressure” is applied on the seawater side, the water molecules in this part pass through the membrane and flow toward the pure water. This phenomenon is known as “reverse osmosis”.
A reverse osmosis system, RO, is a method of pure water production by passing water through a semi-permeable membrane against the osmotic direction, applying a hydrostatic pressure higher than the osmotic pressure. This means that until the minimum pressure on the dissolved water part is lower than the osmotic pressure, the water inside the membrane does not start to permeate from a higher concentration to a lower concentration. The semi-permeable membranes used in RO systems are capable of separating soluble salts up to 99.9%.
- Structure Of Reverse Osmosis Membrane
RO membrane module with spiral configuration is a tightly packed filter in which multiple semipermeable membranes are wrapped around a central tube. The arrangement of the membrane plates, TFC, in a module, is that two TFCs are firmly attached on three sides of the edges, and a special permeate spacer net is placed between each two layers for the flow of filtrated water towards the central pipe. Also, feed spacer nets are used between the attached layers so that the feed can flow uniformly between the TFCs. Therefore, as high-pressure water enters, only pure water passes through the surface of the membrane and the permeate is collected in the central pipe. The concentrate flows out from around the central pipe. The external surface of the module is covered with fiberglass to provide its physical resistance against high pressure and harsh operating conditions.
The main components of the TFC include a non-woven polyester substrate with a thickness of about 100 µm, a polysulfone support layer with a thickness of less than 50 µm, and a selective polyamide layer on the surface with a thickness of about 150-200 nm.
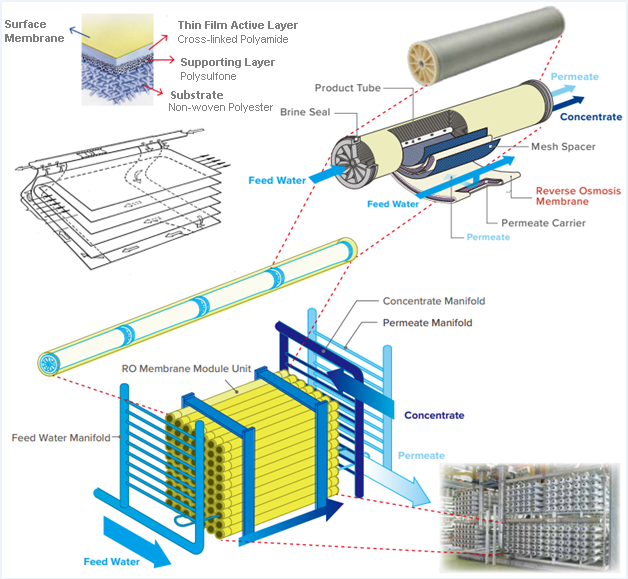
Aromatic polyamide polymer has a stable structure that is highly resistant to chemicals, and easily cleanable. This polymer contains carboxylic acid groups and free amino groups.
The main support for the membrane structure is provided by a strong non-woven substrate. Since the polyester structure is very irregular and porous, a polysulfone layer with microporosity is used as a barrier layer on the surface of the polyester to control the surface pores diameter within 150 Å. Therefore, the active layer with a thickness of 0.2 µm can withstand high pressure due to the polysulfone support. This layer is very resistant to mechanical stress and chemical degradation. The combination of polyester and polysulfone layers is optimized for high permeability at high pressure.
- Reverse Osmosis Membrane Performance
In the design of the modules, the active surface area and the thickness of the feed spacers should be optimized. Generally, membrane efficiency is improved by high active surface area, while a thick feed spacer reduces the potential for fouling. To achieve higher levels of rejection and permeability, the modules are arranged in series inside fiberglass or stainless-steel pressure vessels with high-pressure piping connections on both sides of the modules. Inside the pressure vessels, the exiting concentrate from one element feeds to the next element. Also, the central pipes of the elements are connected to each other and only the purified water flows through these pipes. Pumps are installed before the pressure vessel chambers to create a high-pressure feed flow at about 55 to 60 bar. The speed of the electric motor of pumps at the inlet is controlled to create the desired pressure level. Also, pressure control valves are used on the effluent to adjust the flow rates and create pressure resistance inside the module. In general, the higher concentration of dissolved solids in the water, the higher pressure required to perform the reverse osmosis filtration process. Spiral wound membrane systems manufactured by Pars Avin Tarava have instruments on the pipelines to measure the flow, pressure, and electrical conductivity of the water during filtration.
RO system efficiency is defined as the ratio of product flow to feed and is usually expressed as a percentage. The higher the efficiency, the higher the salt concentration in the downstream stages. As a result, the potential for fouling and scaling would increase in the final elements.
Membrane fouling is a normal phenomenon in most RO systems. Common foulants in the reverse osmosis system are caused by the deposition of calcium carbonate, calcium sulfate, barium sulfate, and strontium sulfate, metal oxides such as iron oxide, manganese oxide, aluminum oxide, silica, colloidal particles, natural or synthetic organic materials such as antiscalant and polyelectrolyte, and biological species such as algae and fungi. Most foulants can be cleaned from the surface of the membrane. On-time washing with the right solution could effectively affect the lifetime and efficiency of the membrane. Also, the contact of the membrane with pollutants such as chlorine will reduce its performance efficiency over time.
The common pretreatment process includes the following steps:
- Separation of particles larger than 5 µm
- Disinfection to destroy the grown biological material
- Use of flocculant or coagulant to enlarge and grow particles to an extent that can be separated by filtration
- Use chemicals to prevent fouling and scaling
- Using an active carbon filter to remove chlorine and other organic compounds
- Final separation of suspended solids using a cartridge filter
Spiral wound membrane modules have the following advantages:
- Accurate separation of substances dissolved in water regardless of their type
- Constant quality of purified water, without extensive changes
- The extremely better quality of purified water than other industrial purification technologies
- Less required maintenance
- Automatic and continuous process
- Low costs compared to distillation or evaporation
- Ability to use a variety of polymer and ceramic materials to manufacture the membrane