The water crisis in Iran has become more complex, although the catastrophe and prolonged global warming droughts have become worryingly challenging. This crisis in Iran has two key factors that are not seen in many international evaluation indicators, but these two components are intensifying the water crisis in Iran. The first problem is the unequal distribution of water in the country. In other words, water resources in Iran are asymmetrically distributed.
The second problem is asymmetric water consumption in different sectors. According to the latest estimates, the agricultural, industrial, and drinking sectors hold 92%, 1.5%, and 6.5% of the total consumption of the country, respectively, while the distribution of consumption in the world is 70%, 22%, and 8%.Therefore, it is understandable that we have more water consumption in the agricultural sector than the real needs. This high consumption in the domestic sectors, which are the agricultural center of Iran, is borne by underground resources.
The water crisis and prolonged droughts caused by global warming have become critically challenging all over the world. This crisis has gained more complex dimensions in Iran with two main components that have not been considered in many international evaluation indexes. The first problem is the unbalanced distribution of water in the country. The second problem is the disproportionate pattern of water consumption in different sectors. According to the latest evaluations, the water consumption of agriculture, industry, and drinking sectors account for 92%, 1.5%, and 6.5 % of the total consumption in the country, respectively. While this pattern in the world is 70%, 22%, and 8% respectively. Therefore, it is obvious that water consumption in the agricultural sector is higher than the actual needs. This shortage in our agricultural sector should be compensated by underground resources.
On the other hand, our industry sector is growing and developing. So, their share in the water resources should be raised to at least 12 times, until reaching an acceptable balance of consumption at the global level. It should be considered that the traditional water sources could not be more developed and also any decrease in water consumption for the agricultural sector is not forecasted. Therefore, Pars Avin Tarava Company is established with the investment of some of the largest mining and industrial companies in the country to strategize solutions related to the sustainable water supply. Currently, these solutions are mainly focused on the use of desalination and water transfer from the southern coastal strip of the country to the industrial regions in the central parts of the country.
Generally, desalination technologies are divided into thermal methods, such as MED, MVC, and MSF, as well as filtration.
MED (Multiple – Effect Distillation) and MSF (Multi- Stage Flash Distillation) take place in a series of stages/ effects based on the principles of evaporation and condensation in the reduced pressures. The significant difference between these two technologies is the method of evaporation and heat transfer. In a MED plant, evaporation is from seawater film in contact with the heat transfer surface. Whereas, in the MSF plant only convective heating of seawater occurs within the tubes and evaporation is from the flashing of a brine flow in each stage.
MVC (Mechanical Vapor Compression) and TVC (Thermal Vapor Compression) are based on the reduction in boiling temperature by reducing pressure. However, in this method, the heating source for evaporation is provided through the compression of vapor rather than the direct exchange of heat from the produced steam. This compression is thermally and mechanically provided.
The figure below shows the share of desalination technologies in the currently installed units worldwide. The most commercially used thermal method is MSF, and its share is about 18% of all available commercial water desalination units. MSF is being used in large commercial units because it is easily manageable with a long operating period.
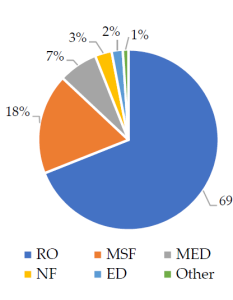
Membrane and filtration technology is a process without a phase change. This technology includes MF, NF, UF, MBs, MD, ED, FO, and RO. Among them, MF and UF systems are not directly used for desalination, but they are extensively used as pre-treatment units. NF is also used for pre-treatment and reveals a better separation capability, compared to MF and UF. In ED technology, ions are driven from the inside of the ion exchange membrane to the electrode with the opposite charge by the driving force of electrical energy. ED is suitable for the desalination of low-concentration solutions.
Membrane Technology | Thermal Technology |
| ||||
RO | ED | TVC | MVC | MED | MSF |
|
Sea water, Brackish water | Brackish water | Sea water, Brackish water | Sea water, Brackish water | Sea water, Brackish water | Sea water, Brackish water | Water type |
Ambient temperature | Ambient temperature | 63-70 | 70-100 | 70 | 90-110 | Operating temperature (°C) |
24000 | 2-145000 | 10000-30000 | 100-3000 | 5000-15000 | 50000-70000 | Unit capacity (m3/day) |
5-9 | 2.6-5.5 | 1.8-1.6 | 7-12 | 1.5-2.5 | 4-6 | Electric energy consumption (kWh/m3) |
——– | ——– | 145-390 | ——– | 230-390 | 190-390 | Thermal energy consumption (kJ/kg) |
———– | ———– | 9.5-25.5 | ——— | 5-8.5 | 9.5-19.5 | Electrical energy equivalent to thermal energy (kWh/m3) |
5-9 | 2.6-5.5 | 11-28 | 7-12 | 6.5-11 | 13.5-25.5 | Total electrical equivalent energy (kWh/m3) |
>500 | 150-500 | 10 | 10 | 10 | 10 | Product Quality TDS (ppm) |
0.52-0.56 | 0.6-1.05 | 0.827 | 2-2.6 | 0.52-1.01 | 0.52-1.75 | Unit product price ($/m3) |
Among all the mentioned technologies, RO, MSF, and MED are the most widely used. The amount of energy consumption in membrane technology is relatively lower. But the cost of the RO product is close to the cost of the thermal technology products due to its higher operating and maintenance costs. In order to reduce the total energy, it is necessary to improve the properties of the membrane or to increase the energy recovery.
In general, there are three strategies for the optimization and improvement of RO performance:
- RO feed water pre-treatment: Filtration of the dissolved and suspended solids in the influent.
- Advanced membrane manufacturing technologies: Novel technologies increase the membrane surface area and permeability and consequently reduce energy and water consumption.
- Flow arrangement: RO systems can be designed in a configuration that the water circulates optimally inside the system and as a result, the amount of water consumption is reduced.
There are several advanced membrane technologies for the optimization of the RO system in specific applications. The implementation of these novel features could reduce energy consumption and increase the rate of water recycling in the system.
- Larger active surface area: In the existing commercial spiral elements, the amount of water production with the same number of pressure vessels increases to 38% by increasing the surface from 320 to 440 ft2.
- Higher permeability: The presence of nanoparticles in TFC enhances the permeability. Nanoparticles in common RO membranes could change the structure of the thin films. As a result, more water permeates and more salt is rejected. These types of membranes operate at lower pressures and higher recovery rates. Therefore, they require less energy for higher feed fluxes. While the cost of making these membranes is slightly higher than conventional membranes, higher permeability can reduce operating costs due to energy savings and lower water consumption.
- Lower biological fouling potential: The feed spacer is responsible for maintaining the water flow channels within TFCs. If the feed water contains a lot of suspended solids, the feed separator can easily become clogged and the flow rate will be greatly reduced. While the feed spacers with a low tendency to biofouling have open channels with a larger cross-sectional area. As a result, the amount of pressure drop in the module, as well as the fouling potential is reduced.